In the current era, characterized by fast technological evolution, the industrial segment has not remained untouched by transformations. One of the fundamental aspects in the management of any plant or factory is maintenance, a key element to ensure the operability and efficiency of equipment.
In this context, a contrast arises between two approaches: traditional industrial maintenance, rooted in conventional methods, and the innovative Maintenance 4.0, driven by the latest technological trends. The transition between these two processes appears to be inevitable. Here, we will explore three fundamental differences between them:
Reactivity vs. Predictability
The traditional maintenance method (TMM) is almost exclusively focused on corrective maintenance and repairs. Here, actions are a consequence of a defective situation that has already occurred. However, the new concept of Maintenance 4.0 aims to intervene before incidents happen. This approach anticipates through the use of sensors and data that can predict quite accurately the life cycle and potential wear or breakages of equipment. Reactivity ceases to be the protagonist, making predictability the main actor.
Top-Notch Technologies
In TMM, rules are governed by the use of manual methods, leading to a significant investment in qualified human resources available at the time of the “emergency.” A transition to 4.0 will reduce costs and time since technologies such as the Internet of Things (IoT), machine learning, and artificial intelligence are incorporated to automate and improve maintenance processes. The use of sensors to monitor the real-time state of machines and assets prevents plant shutdowns for scheduled inspections because information collection is live, allowing the identification of problems and anticipation of solutions.
Utilization and Management of Information
TMM lacks a critical focus on the information collected in each intervention. In fact, information collection is almost nonexistent, as urgency and immediacy eliminate any possibility of data gathering. Maintenance 4.0, on the other hand, relies on the comprehensive analysis of data to create patterns and trends in the behavior of each element and device in the process.
Zero Maintenance Trend
Another major trend in the industry is to use equipment or devices that require minimal maintenance or zero maintenance. This is only possible in equipment with cutting-edge design and raw materials that allow for a robust and durable life cycle.
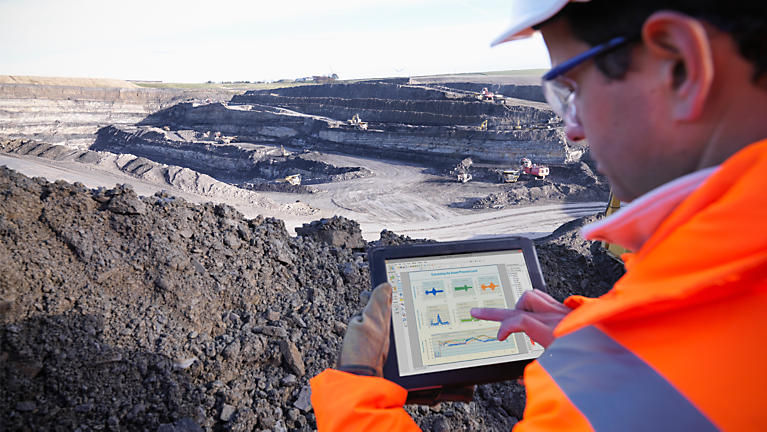
At Fundal, we are dedicated to staying at the forefront of technology, and ARBØR is the result of our desire to be one step ahead. These carbon fiber cardan shafts require no maintenance, do not corrode, and have an extremely longer lifespan compared to steel.
You can find out what ARBØR is suitable for your process line here